Rewind bench
A rewind bench or rewind table is a workspace for rewinding, inspecting, and repairing film. Rewind benches come in many forms, ranging from a pair of hand-crank rewinds clamped to a portable table to purpose-built systems with more advanced features. At the bare minimum, a rewind table should have a pair of rewinds, a light table (either built-in or portable), and room for a splicer and other inspection tools.
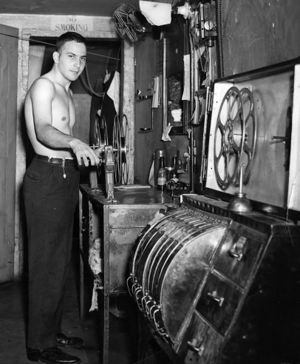
Depending on the hardware installed, the takeup rewind may be referred to as the geared end (when hand-cranked), the drive end, the drive head, or takeup head; the feed rewind may be referred to as the dummy end, brake end, or feed head.
Rewind Types
Rewind tables designed for projection are typically vertically oriented, and are designed to work with film mounted on reels, with either a split reel or flange required to rewind film mounted on cores. Rewinds manufactured for film editing may employ a multi-gang design, in which multiple reels are mounted on the same spindle. Inspection tables designed for archival use are often horizontally oriented flatbeds designed to work with film mounted on cores. In the platter era, some theaters replaced their rewind tables with make-up tables (MUTs) that could rewind film reel-to-reel in addition to spooling to and from the platter.
Vertical rewind tables may have spindles that face the operator (ex., Kelmar tables) or face away from the operator (ex., any hand-crank rewind). The spindles may have clips that fold up to retain the reel on the shaft, or they may be angled so that the reel is kept on the spindle by gravity. Rewinds designed to accommodate multiple reels for film editing commonly employ spring clamps to secure the reel or reels on the shaft.
Some rewinds are designed for use with a single film gauge and reel size, while others can be used for a variety of gauges and reel sizes. Some rewinds have interchangeable spindles, while others use a single spindle with adjustable drive pins to accommodate different reel styles.
Hand-Crank
The most basic rewinds consist of a geared end that is manually driven by a hand crank and a dummy end on which the feed tension is regulated by applying friction to the reel by hand. The dummy end may also have a hand brake or another mechanism to regulate feed tension. The tension settings on hand-crank rewinds can be very rudimentary, such as a spring providing metal-on-metal friction on the back of the feed spindle or a brake paddle with a small piece of leather that is pressed against a wheel on the feed shaft. In many cases more satisfactory results can be achieved by applying friction to the feed reel by hand.
Some have a crank arm on both ends, allowing the film to be wound in either direction. Typically the crank can be disengaged by pulling it towards the operator, separating the crank gear from the shaft gear. While cranking, maintain gentle pressure in the direction of the reel in order to keep the gears engaged.
Hand-crank rewinds may be screwed or bolted onto a rewind table, or they may be portable clamp-on models.
General tips:
- Apply the minimum amount of holdback tension required to prevent the feed reel from racing.
- When using a rewind you’re not familiar with, test the tensioning mechanism with some disposable test film to see if it functions adequately. For rewinds with a hand brake, this is even more essential so that you can familiarize yourself with the proper amount of pressure to apply.
- When applying holdback tension by hand, be creative with your technique.
- If the reel is dirty, hold it from the bottom to avoid dirt falling from the top of the reel onto the film. Clean the reel after the film has been wound off.
- If one of the flanges has a burr on it, hold it by the other flange or apply friction by pressing against the back side of the reel.
- Many people find the most natural holdback technique to be applying friction to the flanges with the palm of your hand. When inspecting film, it may be easier to apply holdback pressure with the back of your hand while holding your thumb and forefinger against the film to check for damage.
- Hand crank rewinds typically have bearings and metal gears that require periodic lubrication. Look for oil points bored into the casting. If the rewind is noisy, feels like it's grinding, or feels like the gearing has more resistance than usual, it is probably overdue for lubrication.
- When stopping to inspect film, disengage the crank arm or, for crank arms without a counterweight, wind it so that the arm is facing down. If left engaged in an upwards position, the weight of the arm may cause it to fall, thereby turning the reel.
- Motorized rewinds are typically better suited for inspection, since the operator’s left hand is free to hold the film without having to also regulate feed tension. When using hand rewinds to transfer film from an improper storage format for which the tension can’t be properly regulated on a motorized rewind (ex., trailers on a 1” core or trailers with no core), consider simply using the hand rewinds to mount the film onto a proper core or reel, and then using motorized rewinds to perform a careful inspection.
Motorized
On many rewind tables, the drive end is motorized. Ideally, the motor should be variable speed and capable of slowly ramping up and ramping down. Single speed motors WILL damage film and should never be used. The motor speed should always be gradually increased and decreased to be gentle on the film.
Motorized rewinds typically have some kind of friction clutch or brake to regulate feed tension. Properly regulating feed tension is even more important with motorized rewinds because of the potential torque that motorized drive ends can apply.
Spindle Types
35mm
The standard American spindle is a 5/16” spindle with a keyed shaft. For large reel playback, an unkeyed 5/16” shaft with a drive pin (also called a drive dog or reel dog) is typically used. Although uncommon, some large 35mm reels use a ½” shaft with a drive pin. In Europe, 9mm spindles with a drive pin are common.
70mm
Spindles designed for 70mm use have a ½” shaft with a drive pin.
16mm
Spindles designed primarily for 16mm use shafts with a square base. Most 16mm reels can be rewound using a 5/16” keyed shaft.
Alignment
Rewinds should be aligned so that films spools between them as evenly as possible. To test alignment, use two house reels that you know to be true (no wobble or bent flanges). Spool test film between them a number of times to make sure the film isn’t kissing against the flanges. Adjust the position of the rewinds as necessary.
It was once common practice in projection booths and film exchanges to intentionally misalign rewinds so that the flange of the take-up reel would guide the film, ensuring a smooth wind. This should be avoided because it can damage the film, especially if there are any burrs on the flanges.
However, even on a perfectly aligned rewind table, the lateral alignment of the film path will vary based on the style of reel or film transfer flange on which the film is mounted, with the inboard film edge offset from the back of the spindle by the depth of the flange. For example, an aluminum house reel has thicker flanges than a split reel, so the film on the house reel will be slightly further away from the back of the spindle than the film on the split reel. It is important to understand this bias when winding film between reels of different types. When spooling from a house reel to a split reel or shipping reel, the film may kiss against the outboard edge. When spooling from a split reel or shipping reel to a house reel, the film may kiss against the inboard edge.
Best Practices
No matter what type of rewind equipment you are using, it is essential that even speed and tension be maintained on the take up and feed reels at all times. Always be checking your reels and spindles to make sure they are true and not bent or warped. If you're using a Kelmar table check to make sure the pads aren't worn down. The rewind table is one of the main places that prints are damaged! Never leave winding film unattended.
- Be very careful when winding film that is loosely wound onto another reel, if too much tension is put on the film it will become cinched. THIS DAMAGE IS IRREVERSIBLE as dirt is embedded into the emulsion.
- Keep it Clean: your rewind table is not your desk. We know booths can be very small, but keep your rewind table tidy and free of dust, and give yourself room to work.
- Tension: check your tension, change it depending on film gauge, reel size, etc.
- Check the pads often on the Kelmar rewind arm, if they get worn down they need to be replaced. Do not get oil on the pads! The same goes for the Kelmar arms on your projector.
- Having trouble getting a warped film to wind? Trying winding it over/over or under/under. Make sure it’s not rubbing against the side of the reel.
- Check for bent spindles. Can be straightened out by a machinist, or you can buy new ones. Bouncing can mean the bearings are going bad or you need to replace the pad.
- Speed - Slower is better. When inspecting film, you should be winding it slowly enough that when you stop winding after feeling damage, you don't have to rewind the film to find the damaged section. If you're overshooting, you're winding it too fast.
- When using Kelmar tables, 20% motor power is typically appropriate for inspection, while 30% is appropriate for rewinding. Do not exceed 40%.
- Rewinding onto reels that are out of round/not true (slowly but surely…)
- Auto-rewind rollers - Using these rollers can sometimes help to get a tighter wind on warped prints. Make sure the roller is clean if you use it. Never leave rewind bench unattended while film is rewinding.
- Common problems: telescoping and cinching on loosely wound prints, proud edges (when some edges are raised or sticking out of the reel). Never ship a print with proud edges on the reel, they can be crushed easily and cause edge damage.
- Tension winds: Learn how to do a tension wind (i.e wind the film onto the core of the reel WITHOUT putting the end of the film into the slots. NEVER tape the film to the reel or core. Use a tension wind for the take up reels on your projectors as well.
See Also
External Links
- Kelmar Systems, manufacturers of motorized vertical rewinds. Rewind tables and accessories here
- Kinoton FVT HD Inspection Table - Sprocket-driven inspection table with a variable wrap to compensate for shrunken film.